About Enlighted
Enlighted is a smart building infrastructure company that uses IoT lighting technology to operate, orchestrate, and optimize sustainable spaces. By intelligently connecting and managing thousands of sensors and smart devices throughout any built environment, customers gain real-time, data-driven insights about the use of space, and the movement of people and things through those spaces, to make complex operation and management decisions easier and more effectively.
* Enlighted is part of Building Robotics Inc., a Siemens company.
Stefan Schwab joined Enlighted as CEO in 2018. Prior to Enlighted, he was the Executive General Manager for Siemens Building Technologies in Australia and New Zealand, where he led business transformation by empowering people and increasing customer centricity.
Challenges of adopting smart technologies in manufacturing
Despite persuasive evidence of the benefits of digital transformation, many manufacturers are still hesitant about IoT adoption. The primary reason is that it looks like a heavy lift for them, in terms of cost, effort, and possible disruption. This fear actually stops them from automating their processes and bringing smart technologies to their production environments. Thus, a lot of IoT initiatives crash against an insurmountable number of presumed challenges. In reality, the challenges relate to the integration with third-party platforms and retraining management staff. In other words, the main barrier on the way to IoT adoption in manufacturing is the lack of understanding about the available solutions and the importance of smart technologies for production growth. Some companies give up without trying, or simply choose technologies that are neither suitable nor valuable for their business.
The positive news is that the collaboration and data exchange in the industry will enable progress. Manufacturers must connect many different systems and transfer the corresponding knowledge to meet modern requirements for lower operations costs and speed to market. Those who embrace IoT solutions for a variety of manufacturing use cases can successfully gain a competitive edge.
Wired, on-premises solutions: an indicator of risk-aversion
The use of cloud technologies in manufacturing is another education opportunity. Today, some manufacturing companies don’t trust wireless communications. They are skeptical about everything related to cloud-based solutions and prefer to rely on isolated networks with on-premises servers and wired data transfers. This comes from a legitimate fear of production interruption and real revenue loss.
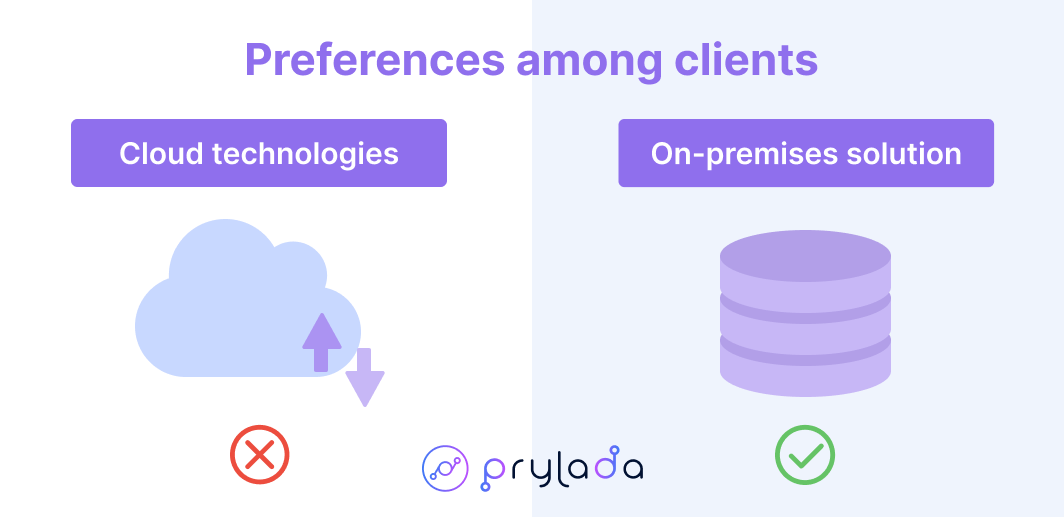
What influences this choice? Many manufacturers are accustomed to thinking of wireless networks as insecure and unstable, grounding their opinion on outdated theory. Or, they are simply risk averse, unwilling to explore new innovations, to employ industry tested standards or to understand the benefits of cloud computing. Fortunately, modern technologies can demonstrate that cloud solutions have made significant breakthroughs in both security and reliability. Edge technologies can mitigate the risks of cloud connection loss, and companies can test and ensure that there’s no interference around wireless networks. Moreover, cloud technologies provide scalability, can more easily facility software updates, and can seamlessly serve multi-geo sites.
Overcoming the fear of the IoT adoption through demonstrated value
The most straightforward way to bring automation and smart technologies to manufacturing is through education and proof of value. Customers are open to new technologies when it solves a problem, reduces costs or provides a way to speed production and efficiency. If the suggested solution is a “nice to have”, then it will be challenging to persuade a company to implement. If, on the other hand, competitors are leveraging these same technologies to gain a market advantage, the fear of the unknown quickly gives way to legitimate curiosity and a willingness to listen.

It is crucial to provide manufacturers with proven implementations of IoT technology and viable problem-solving options through customer references and examples. This not only shortens the timeline for digital transformation, but also prepares them for any challenges. Seeing demonstrated outcomes from peers in their spaces can empower companies and enable them to move forward more rapidly with management approvals for IoT implementations.
Other factors that influence decision-making
COVID-19 brought changes to the manufacturing industry. In particular, the pandemic shifted the buyer persona on the customer side, making it more complex for IoT vendors to approach. Because of supply chain issues and labor shortages, the entire C-Suite became intimately involved in floor level issues and decisions. This resulted in an increased number of stakeholders and a more complex and lengthened process for change.
This new and increased set of buyers means that IoT technology providers need to articulate the benefits of IoT solutions to a broader set of influencers across departments and functions within each company. Despite the increased interest and demand for smart technologies in the market, the decision-making process became slower as multiple stakeholders need to understand the risks, agree on projected value benefits and weigh these against other company initiatives.
Significant losses from the unexpected consequences of the pandemic made industrial companies re-think their current approach to business. With that came a desire to be more resilient to such kind of force-majeure circumstances, by optimizing existing processes and minimizing their dependence on external conditions. These tendencies play well for IoT implementations, which can bring some of these efficiencies.
Commitments toward sustainability goals towards 2030 are another driving factor towards factory modernization. New IoT technologies can reduce energy use and carbon emissions when deployed across both manufacturing sites and their associated supporting offices. These upgrades consist of a mix of upgrading existing facilities and building new, modern, energy efficient ones. The focus on sustainability can become a driving force for wider adoption of IoT technologies and make the manufacturing industry smarter, more efficient, and sustainable, as well as improve the wellbeing of its employees.
US market vs European market in adoption of digital technologies
The rate of adoption of digital technologies and cloud solutions also varies geographically. The leading position in this category is still occupied by US firms.
According to the European Investment Bank (EIB) Investment Report 2019/2020, the EU firms are less likely to innovate or to adopt new technologies than US firms. Only 66% of manufacturing firms in the European Union, compared to 78% in the United States, report having adopted at least one digital technology (Figure 1). Using data on specific digital technologies in the four sectors suggests that this gap is driven by lower adoption rates of Internet of Things (IoT) technologies.
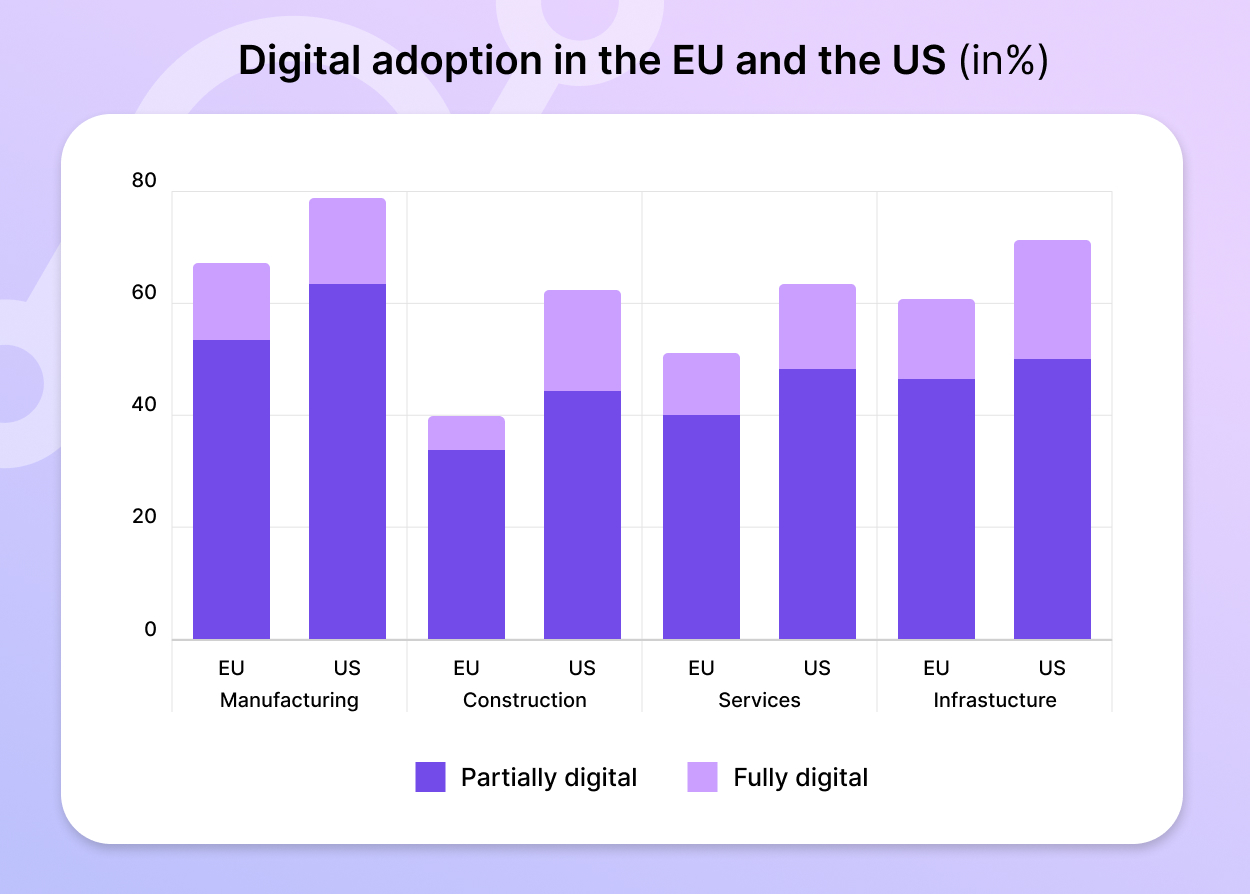
Source: EIB Investment Survey (EIBIS wave 2019).
Note: The figure is based on a survey asking firms to answer questions on four different digital technologies: whether they have heard about them, not heard about them, implemented them in parts of their business, or whether their entire business is organized around them. A firm is identified as ‘partially digital’ if at least one digital technology was implemented in parts of the business, and ‘fully digital’ if the entire business is organized around at least one digital technology. Firms are weighted using value added.
According to the EIB Investment Report 2022/2023, the COVID-19 crisis made European firms to change their vector for digitalization. More than half of EU firms, (53%), said they took steps to become more digital, for example, by providing services online (Figure 2).
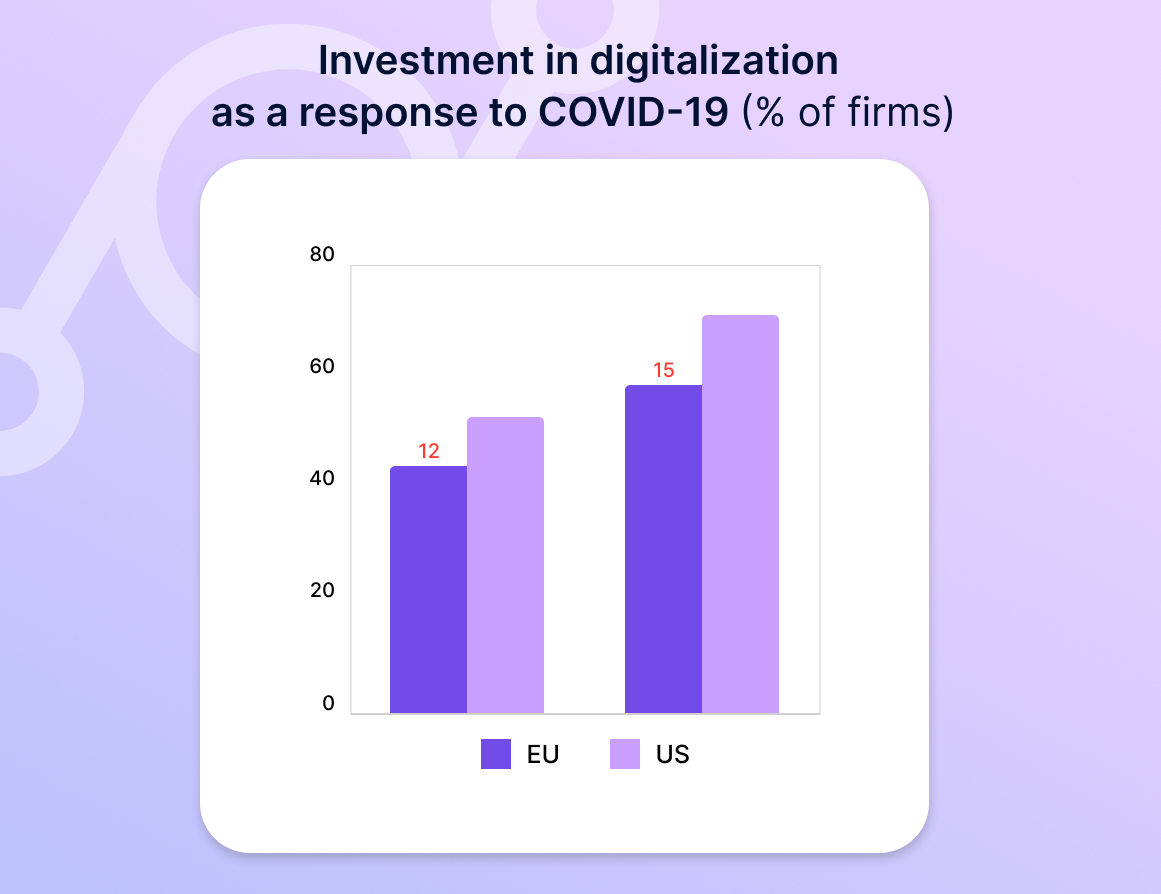
Source: EIBIS 2021-2022.
Note: The number over the bars indicate differences in percentage points between the United States and the European Union.
While European firms made big gains, the share of firms that invested in digitalization as a response to the pandemic was still higher in the United States. This gap is driven by greater US investment in machinery and equipment and innovation, particularly in information and communication technology equipment and intellectual property.
The European Union, however, has been closing the gap with the United States on the adoption of advanced digital technologies over the past four years. 69% of EU firms implemented advanced digital technologies in 2022, compared with 71% in the United States (Figure 3).
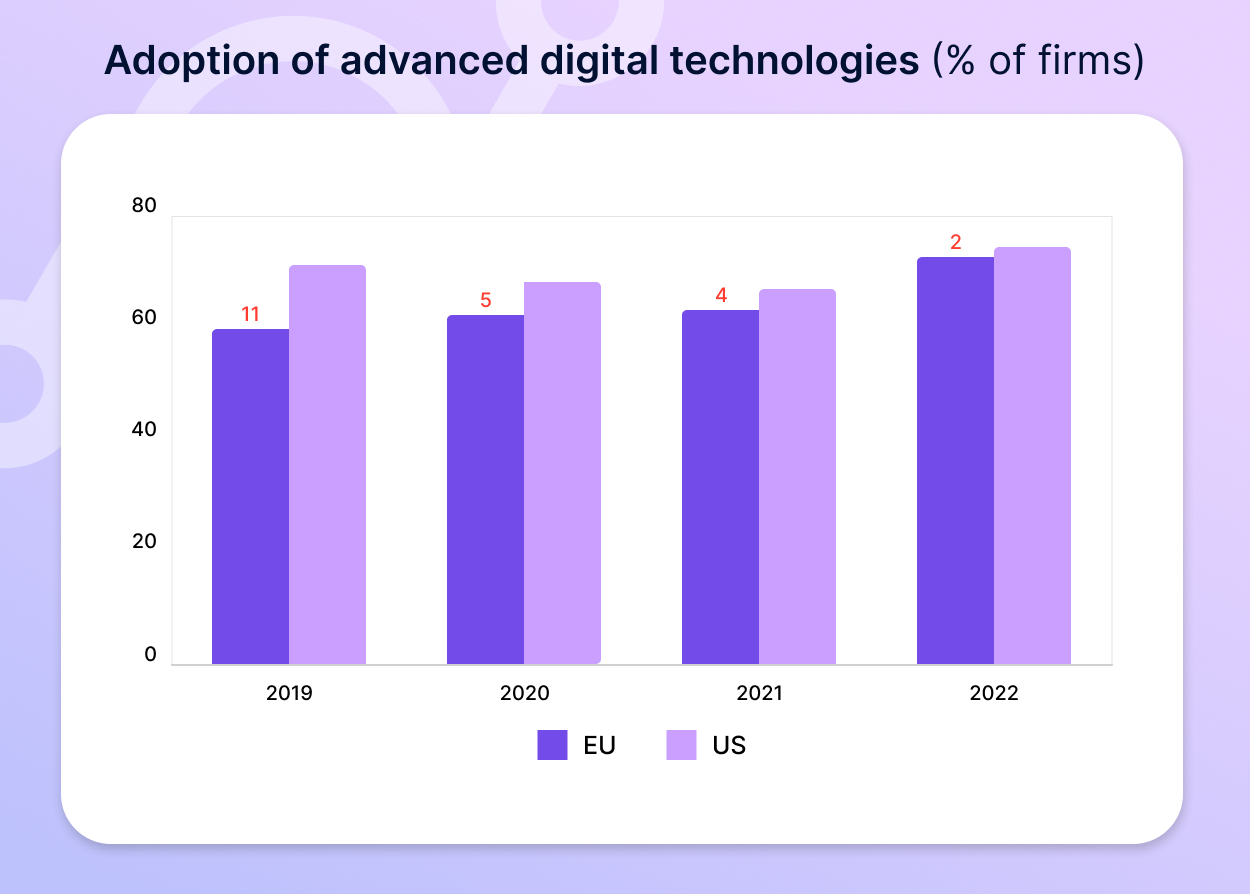
Source: EIBIS 2019-2022.
Note: The number over the bars indicate differences in percentage points between the United States and the European Union. A firm is identified as having adopted an “advanced digital technology” if at least one digital technology specific to its sector was implemented in parts of the business and/or if the entire business is organized around at least one digital technology.
Benefits of smart technologies for manufacturers
The most obvious benefits of smart technologies for manufacturers are in the achievement of sustainability goals, reduction of energy costs, increased operational efficiencies and greater throughput and profitability. Based on the accurate data from connected devices, manufacturers can review every production process to analyze, recalibrate and optimize it. They can easily identify energy savings and reduce untapped resources, thus increasing revenues and opening new opportunities for growth.
For industrial companies just starting out their digital transformation journey, the best place to begin is to understand how IoT technologies can transform their operations:
- Reduced costs and downtime - Data from sensors and edge devices allows operators and engineers to timely detect improper behavior of the equipment and prevent its failures (preventive maintenance instead of time-consuming repairs). This enables them to upgrade the existing critical assets rather than invest efforts, time, and money in additional digital and physical resources. Moreover, tracking spare parts and materials significantly facilitates supply management, which also contributes to enhancing efficiency and uptime.
- Minimized gaps between planned and actual production results - Optimized production processes, increased uptime, and proper management help speed production without delays.
- Improved quality of the final products - Reducing downtime and maintenance costs allows manufacturers to focus on more sophisticated tasks, including products. This looks even more feasible with smart technologies, since automated and controllable processes minimize the risks of human errors.
- Centralized data analysis - With intelligent data collection and management, it’s possible to organize a common knowledge base and data storage across the factory and across multiple locations by leveraging cloud technologies.
Stefan Schwab shared some examples of how Enlighted helps its customers optimize facility management with their lighting control sensors combined with new IoT technologies. The sensors can track different assets with the data they collect through the Location Intelligence solution.
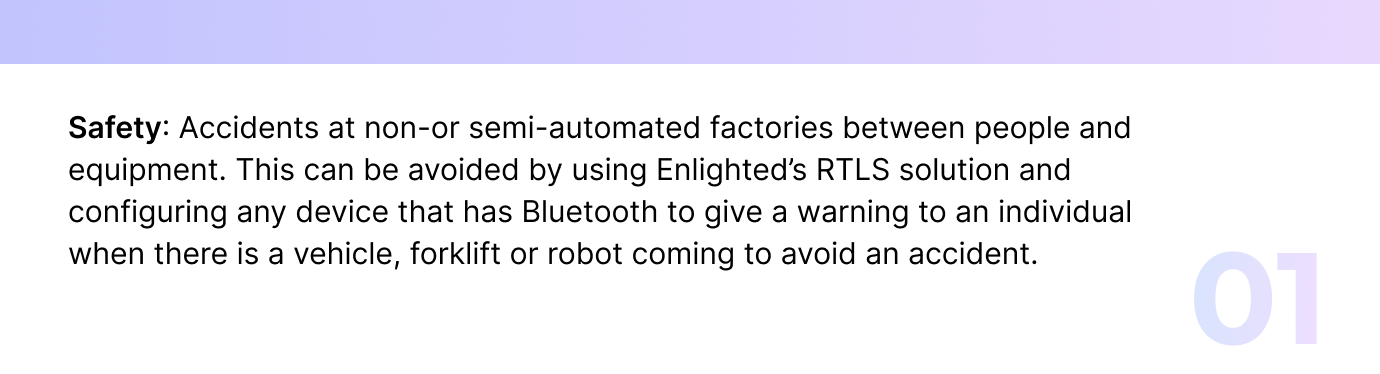
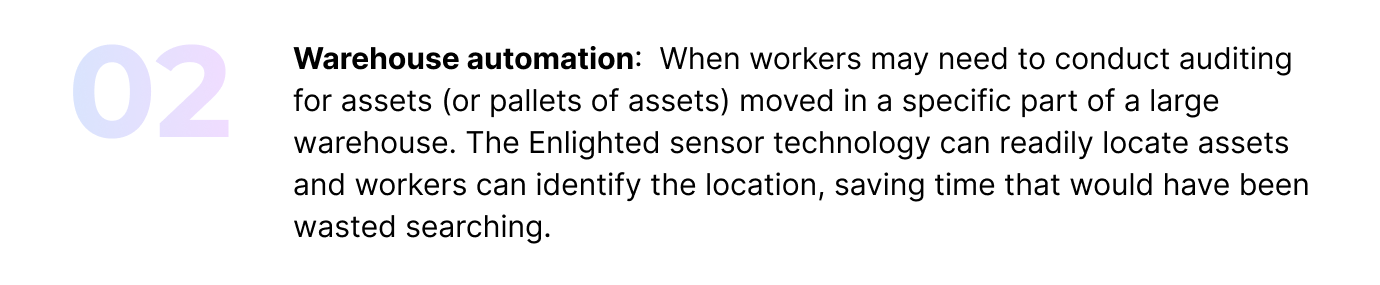
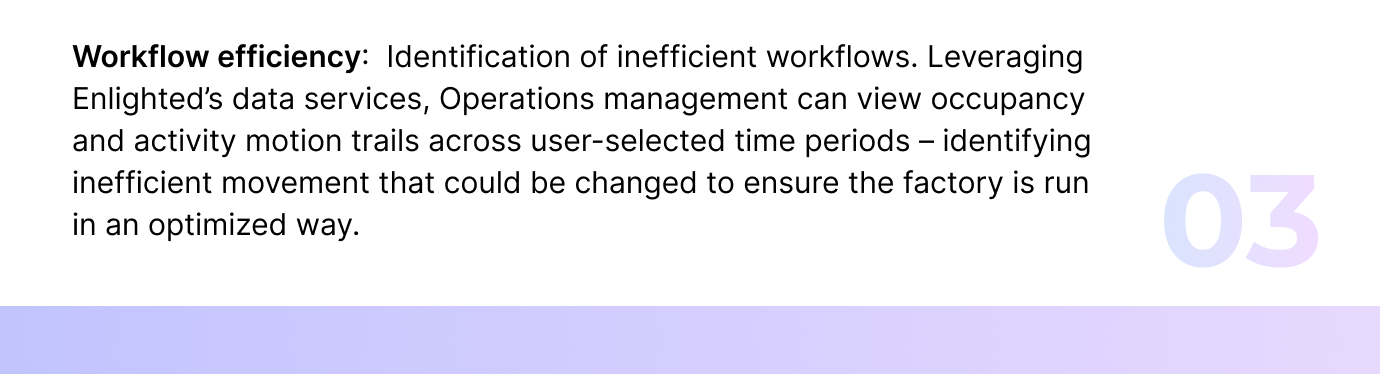
Additional value for clients through partnership network
Integration with third-party systems for extended functionality, or partnership networks, provides additional value for clients and is essential to create a smart manufacturing facility. For example, if a company has a BMS system in place, they can integrate additional building IoT technologies and other systems that could include security, air quality or crisis management. Being BMS vendor agnostic is important, as many manufacturers leverage different systems in different locations.
Conclusion
In conclusion, the decision-making process for adopting smart technologies in manufacturing is influenced by various factors. The challenges of cost, effort, and potential disruption often deter manufacturers from embracing IoT adoption, but education and proof of value can help overcome these fears. The preference for on-premises solutions and the perception of wireless networks as insecure also play a role in decision-making, but advancements in cloud technologies, edge computing, and network security can address these concerns.
The COVID-19 pandemic has led to a more complex decision-making landscape, with multiple stakeholders and a focus on resilience and sustainability. Convincing these new influencers of the benefits of smart technologies: achieving sustainability goals, reducing energy costs, increasing operational efficiencies, and improving product quality will be key for the manufacturing industry to embrace the use of IoT technologies. Those that make the move sooner rather than later will gain early mover advantage and a competitive edge.