The article is based on the written responses attributed to Tom Richter, the global head of discrete and process manufacturing verticals for digital industries at Nokia. This interview is one of the series of interviews with manufacturing experts carried out by Prylada.
About Nokia
Nokia Corporation is a Finnish multinational telecommunications and information technology corporation. From 5G smart factories to transformed digital supply chain and logistics operations, Nokia works with manufacturers to find the solutions to realize their Industry 4.0 operation.
Manufacturing market changes in adaptation to digital technologies over the last 5 years
It’s worth emphasizing that the adaptation to emerging digital technologies for manufacturing must be evaluated within the context of their benefits for the respective businesses. Certainly, over the last five years, businesses have been forced to respond and adjust to the fast-paced changes and disruptions within the markets they serve–from social user trends affecting consumer behaviors, to significant environmental and geopolitical events.
The organizations that have initiated their digitalization programs over this period are more likely to gain continued competitive advantage and market success in the future. Among the most implemented digital technologies are digitally-enabled sustainability solutions, digital twin, autonomous mobile robots, augmented reality, AI and machine learning.
Factors driving the manufacturing digitalization
The consumer choice leading to personalization of purchased goods, the keenest prices, and the best delivery times has pushed manufacturing companies to re-think their working approach and enhance productivity by implementing digital technologies.
In addition, the world events over this period have highlighted just how important it is to have resilient and responsive supply-chains. The environmental, social, and corporate governance (ESG) demands continued to make a fundamental influence on organizational strategy and performance.
Digitalization benefits for manufacturing
Digitalization is an essential element in addressing such organizational challenges as strive for resilient supply-chains, mass customization, smart and integrated warehousing, smart energy management, factory asset intelligence, augmented workforce, dynamic scheduling, greater innovation and faster time-to-market, safe and sustainable production, optimization and yield, service leadership and customer satisfaction.
Most manufacturing digitalization programs are likely to be within brownfield–as opposed to greenfield–sites and therefore augmenting incumbent systems with new seamless, scalable and simple technologies. It is essential that the needs of both operational technology (OT) and information technology (IT) are facilitated, and that there is an effective convergence platform for the integration of relevant processes. Such platform ensures the digital transformation success for manufacturers and requires the right data as an essential starting point.
Data is critical for all digital transformation journeys, and this starts with the underpinning connectivity of assets, people, machinery, and process–so that they effectively work as a single body. The integration of OT and IT networks is fundamental in this respect. For example, when a plant level control is handled by incumbent wired systems, while the condition monitoring and connected worker systems augment the existing connectivity with wireless systems. The choice of solutions should be driven by their fitness for the purpose of the relevant networking technologies.
Having mutual insight and input to respective OT and IT functions, operations, and performance allows the respective teams to extend their impact on overall manufacturing business objectives, like productivity, flexibility, and quality.
Points to consider before initiating digitalization
Despite the multiple advantages of digitization, there are certain points that manufacturing companies must therefore consider when evaluating the viability of new technologies. Among them are such typical questions as:
.png)
Importantly, the answers to these questions must also include the impact of any change on the essential manufacturing pillars, such as worker safety, security, legislation, and quality. The implementation of new technologies must therefore be solution-led, with collaboration, innovation, and digitalization at the core of these solution programs.
Preference to wired and on-premises solutions in manufacturing: the reason
The crucial factor for manufacturing is that it is able to respond to market demands, challenges and opportunities as part of its overall organization’s ecosystem. Therefore, the choice of adopted technologies should be judged by what addresses the business needs in the most effective way.
In the context of wired, wireless and cloud solutions, these should be aligned to the provision of applications where they are best suited. In practice, it will be the combination of the technologies that provides the optimum solutions.
.png)
We may also highlight that standardization and product evolution in all areas tend to close the gap between OT- and IT-specific architectures and features. This can make wireless, cloud, and distributed solutions suitable for hard-core industrial application scenarios in the future.
.png)

The main challenges of adopting digital technologies
The rapid evolution of data driven analytics requires ever more data about all sorts of “assets” (including workers) to feed intelligent algorithms. The data use is not limited to machine control, but is required for a whole lot of other use cases. Among them are supply chain management (of products, materials, accessories), energy and environmental monitoring, new holistic safety schemes, and so on.
Large amounts of data lead to the challenges of integrating, upgrading, and upskilling. This also requires the adoption of new technologies like wireless connectivity to enable legacy equipment without touching certified cabling. Often, these machines and assets reside in distinct functional ‘silos’, and therefore wireless connectivity is typically the most effective way to collect necessary data whilst transcending such operational barriers. There are also more and more mobile assets (let alone workers) that need to be included in the data exchange. Wireless connectivity in this case helps achieve easy flexibility, accessibility, and adaptability.
When integrating any new technology, there are hurdles to overcome. For intelligent asset and machine monitoring, there are two challenges, The first involves integrating and upgrading legacy equipment to be compatible with new technology–ultimately enabling the full potential of Industry 4.0. The seconds supposes reskilling workers to ensure they can effectively monitor, use and benefit from intelligence monitoring systems.
Point-blank, it is difficult to get the full picture of what an asset or a manufacturing plant is doing when not all of the components are compatible with the existing software or hardware. By upgrading legacy equipment, manufacturers can have a more comprehensive look at the issue at hand and can more effectively decipher where things can be done more efficiently. Of course, you also need employees who know how to manage these new tools as well as read and assess these results, which is where reskilling the workforce comes in.
For smaller manufacturers, the upfront investment in new technology is often intimidating. However, neither digital transformation nor employee transformation happens overnight. To really make the most of the investment and reap the benefits of intelligent asset and machine monitoring, network access to data from legacy equipment needs to be replaced or enhanced and workers need to be continuously reskilled.
Readiness to talk about digitalization
We found that companies are very open to talking about digitalization and adopting smart technology now. As a part of our Industry 4.0 Maturity Index report, we surveyed 500 individuals in various vertical markets and found that industry average scores found to be 66 out of 100 for technology maturity and 68.8 for use case deployment maturity. Responses showed electronics and appliance manufacturers are forging ahead with scores of 73.1 and 79.5 respectively.
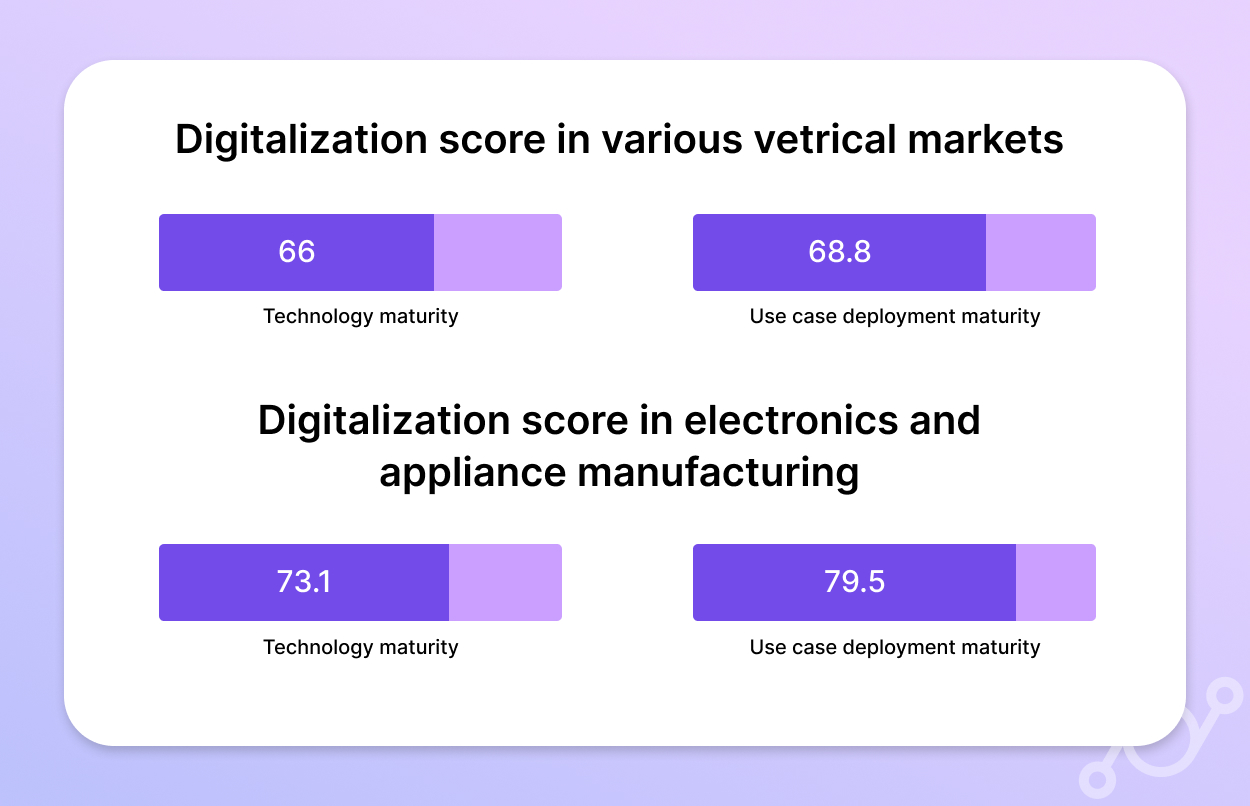
The survey also found that electronics and appliance manufacturers are leading the way in Industry 4.0 technology investments and use case deployments with maturity scores of 73.1 and 79.5 out of 100, respectively.
The bottom line
The increasing demand for adopting digital technologies and benefits that manufacturing companies can get from them drive the overall digitalization growth. The choice of technology and its implementation option yet depends on what combination will address the business needs in the most effective way.
In general, it seems clear that manufacturers know that adoption of digital technologies is an important part of their journey. The question is now “how” and “when” they will get there.