Regardless of the type of testing we perform–be it initial hardware tests, regression tests, load tests, or post-production validation tests–we always strive to answer the question of how to make it more efficient. Efficient in this context means minimizing manual work, maximizing hardware and software requirements coverage, and ensuring thorough test results logging. The logging in turn enables proper failure analysis and production quality tracking and analysis.
Challenges of manual hardware testing
Modern devices are complex, and it is crucial to ensure that both hardware and software perform as intended before they reach the customer. While software testing often requires nothing more than manual labor, hardware and firmware testing can be more challenging.
Hardware and firmware operation depends on multiple factors, some predictable and others unpredictable. To ensure that customers do not encounter any unpleasant surprises, we must ideally test our devices under all possible conditions. These conditions can be environmental, such as temperature, humidity, light, vibration, and electromagnetic waves, or they can involve interaction with the surrounding world if our device is part of a larger system.
We must consider how quickly the battery discharges, how our device reacts to border conditions, and how the design tolerates hardware component parameter deviations. There are countless questions to consider, multiplied by the number of devices in production and the number of scenarios. Almost every parameter we would like to control is not binary, but it can change within some range.
In other words, manual hardware testing is only suitable for smoke tests, which are performed when we power on our device for the first time in a plug-and-play mode. Attempting to apply manual hardware testing to even a 200-piece batch would be impractical and time-consuming. It would be more efficient to use automated testing methods to ensure that the hardware and software perform properly.
However, automatic testing implies additional costs due to the following factors:
1. Firstly, hardware should be designed for tests. For instance, it should contain test points, enabling quick connection of a device under test (DUT) to a test bed equipped with spring loaded pogo pins.
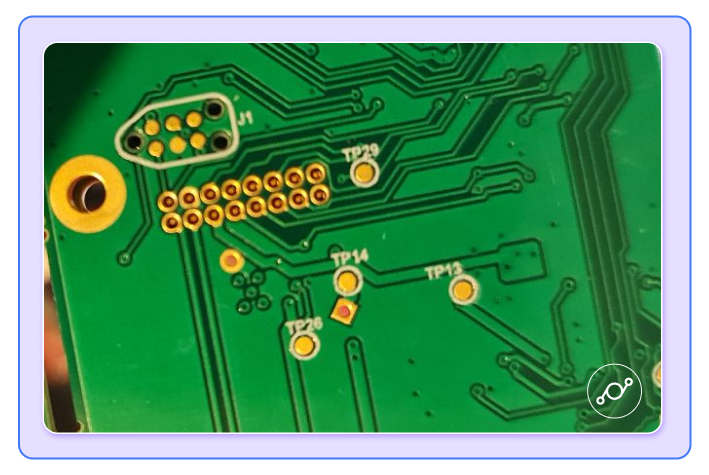
2. Secondly, automated testing requires the creation of a test bed itself, with pogo pins at the right points. These pins should be wired to the sockets, letting them connect to a testbench which generates test signals and reads the DUT responses.
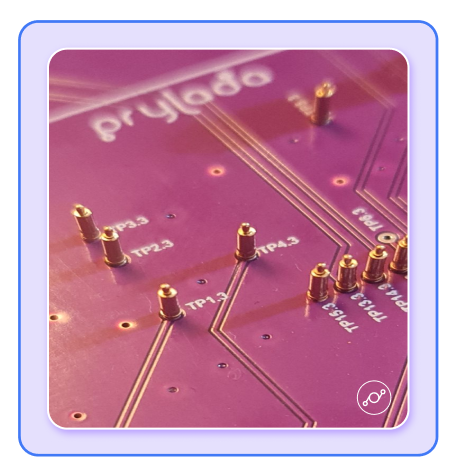
3. Thirdly, testbenches vary in functionality and price. They should be sufficient for particular test needs on the one hand, and highly flexible and modular enough to be easily adjusted for further design solutions on the other. They may equally contain simple analogue and digital inputs and outputs, and industrial bus controllers, software controlled power supplies, complex DSP modules, etc. But the main purpose of all testbenches is the same–to create a real-world environment digital twin for DUT.
What is hardware-in-the-loop (HIL) testing?
Hardware-in-the-loop (HIL) testing is a method of testing and verifying complicated hardware systems using specially equipped testbenches. HIL testing allows you to test your hardware in a simulated environment that closely resembles the real world, causing the device under test to believe that it is reacting to real-world conditions.
The real-world conditions are reproduced with the help of automated test scenarios that are predefined and run from a testing software. By imitating the real-world environment, you can test your hardware under a wide range of settings and scenarios, which is not impractical with manual testing alone.
The primary goal of HIL testing is to assist you in optimizing your hardware design and ensuring that it meets the necessary criteria. This can also assist you in identifying difficulties early in the development process, reducing the risk of costly flaws later on.
Benefits of HIL, or why all manufacturing companies need it
- HIL testing can simulate hundreds or thousands of scenarios without the time and costs needed for manual hardware testing.
- HIL testing can simulate conditions that would be too dangerous or impractical to reproduce manually.
- HIL tests are repeatable.
- The HIL testing process is highly automated and can accommodate multithreading, allowing numerous tests to run concurrently, which speeds up the development process.
- HIL allows for frequent firmware releases with predictable system behavior.
- While HIL testing occurs later in the development process than software testing, it still makes part of the CI/CD process and allows developers to identify any faults before sending the product to the customer.
HIL testing using the Probeberry Testbench
The Probeberry Testbench is designed to execute automated test scenarios on any type of hardware. The testbench enables you to create all the possible conditions your device can work in, to test the maximum hardware requirements coverage. With the test results logging and reporting, you can make proper failure analysis and production quality tracking.
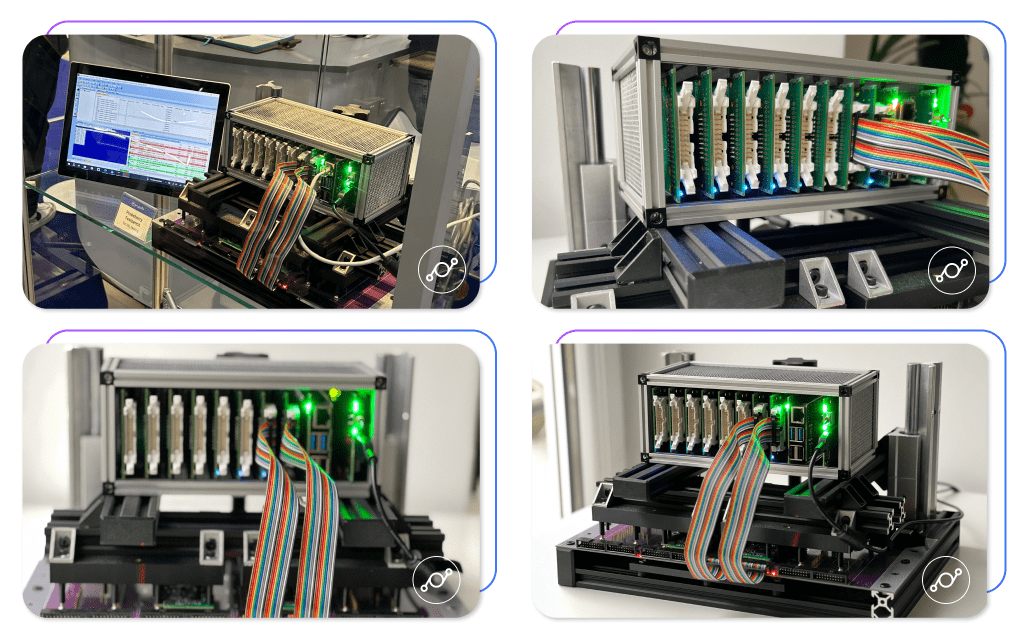
By design, the Probeberry Testbench consists of eight modules that are controlled by a test automation software running on a PC. The software allows creating, managing, and executing predefined test scenarios on a connected DUT. The test results are then reported either to the Prylada Cloud or a customer’s server.
.png)
The testbench modules provide different options of communicating with a DUT, including:
• Analog/digital input/output
Eight on-the-fly reconfigurable channels that can be programmed to perform as: AIO 4-20 mA, 0-10V; digital input (including dry contact, with adjustable 500mV-16V threshold); RTD measurement.
• Interfaces
RS232; RS485 with MODBUS support; I2C with SMBUS support; SDI12.
• ModBus
Standart Protocol to program inputs/outputs.
• Analog multiplexer
Four analog multiplexers 1:4.
The modules receive and send input/output data in real-time. Every module reads data from multiple sensors, connected directly or via a bus, or it controls DUTs, either connected directly to a gateway or receiving setpoints via a serial bus or a wireless network.
Competitive advantages of the Probeberry Testbench
• MODULAR ARCHITECTURE
The platform modular architecture allows you to easily scale the Probeberry to fit your project needs.
• POWERED BY RASPBERRY PI
Our engineers ensure high reliability and quality of every component used by partnering with the industry leaders like Raspberry Pi. You can find the Probeberry Testbench in the catalogue of powered by Raspberry Pi products (please apply the filters of “SBCs” and “Industrial control/applications”).
• STANDARD HARDWARE
Popular off-the-shelf microcontrollers are used to provide you with extra flexibility and connectivity options.
• SOFTWARE VARIETY
Due to the open nature of the platform, Probeberry can be controlled by the Probeberry software, native Arduino or Raspberry software, or any custom control software.
• CLOUD AUTOMATION
Cloud automation enables communication with one or multiple Probeberry instances, to gather data, control processes, display historical or actual data, and send reports.
• IN-HOUSE DEVELOPMENT
All the Probeberry modules are developed internally by the Prylada team.
At Prylada, we are dedicated to solving real customer problems through a highly personalized approach. Our goal is to help you automate hardware testing and optimize your physical asset monitoring by developing a tailored solution that meets your specific needs.
If you’re interested in learning more about our services, please feel free to contact us at contact@prylada.com. We offer a free in-depth consultation to help you better understand how our solutions can benefit your business. Once we receive your request, we will guide you through the Prylada tour based on the implemented projects, thus creating a better understanding of the solution capabilities.